1. 사출 공정
- 형체 공정 : 금형이 닫혀 형체결이 완료되기까지의 공정
- 사출 및 보압 공정 : 스크루 전진에 의해 용융수지가 노즐을 통해 유입되어 금형 내에서 성형되는 공정
- 냉각 및 가소화 공정 : 성형품이 냉각되는 공정과 동시에 용융수지가 스크류 회전에 의해 노줄 전단부로 이동됨
- 형개 공정 : 성형품을 취출 하기 위해 체결되었던 금형을 여는 공정
- 취출 공정 : 금형 코어에 남아있는 성형품을 이형, 취출 시키는 공정
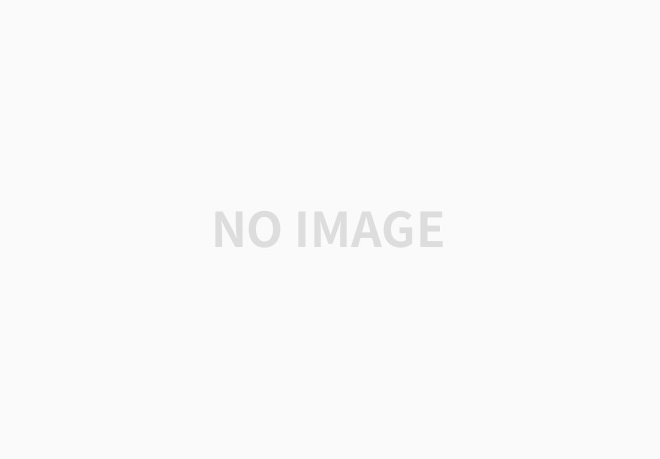
사출
- 스크루의 구동 장치에 연결된 유압 실린더나 서브 모터가 용융된 수지를 스프루 부싱을 통해 캐비티 내로 밀어 넣는 충전과정(filling stage)이다.
- 스크루는 회전하지 않고 수지가 금형 내로 들어갈 수 있도록 앞으로 전진을 하게 된다.
- 이 기간 동안에 소요되는 시간을 사출 시간이라 정의를 하고 있으며, 스크루가 전진하는 속도는 조절장치에 의해서 컨트롤이 된다.
- 역류 방지 밸브에 의해 용융 수지의 역류를 방지한다.
보압
- 보압 시간이라고 일컬어지는 시간 동안, 노즐에서 일정한 압력을 유지하는 과정이다.
- 이 단계 동안에 금형이 식으면서 생기는 부피 수축을 보상하기 위하여 고압으로 여분의 수지를 밀어 넣는 과정이다.
- 제품의 성형 수축률이나 sink mark, 잔류 응력 등에 영향을 미친다.
- 보압은 사출압의 50~90%, 또는 보압 절환 시점의 캐비티 내압으로 설정한다.
- 보압 시간은 게이트가 고화되는 시간까지 설정한다.
냉각/계량
- 금형 내의 용융 수지가 취출이 가능한 온도까지 냉각하는 과정이다.
- 고화가 시작되면 금형을 체결하는 힘은 작아도 좋기 때문에 금형이 닫힌 상태에서 형 조임 실린더는 저압으로 된다. 이 고화 시간을 이용하여 사출 장치는 다음 사이클의 준비로서 수지를 용융시키기 위하여 가소화 공정에 들어간다. 이 공정에서는 스크루를 전동기 또는 유압 모터로 회전시킨다.
- 스크루가 회전하면 새로운 수지는 호퍼로부터 스크류 안으로 들어오게 된다.
- 스크류 안으로 들어온 수지는 노즐 쪽으로 보내지게 되며, 이 과정에서 압축되고 밴드 히터로 가열되어 용융되며 노즐 부분에 저장된다. 용융된 수지가 한 곳에 모이기 때문에 그 압력에 의하여 스크루는 후퇴하며 수지 계량용 리미트 스위치를 누르기까지 후퇴가 계속되다. 이것을 계량 스트로크라 말하며 사출 하는 양은 이 스트로크로 결정된다.
취출
- 금형 열림 완료 부근에서 금형은 사출기에 고정되어 있는 이젝터 로드에 닿아 성형품을 밀어낸다.
- 사출 장치는 보통 사출 전에 금형의 스프루에 터치하며 시출이 끝나면 후퇴하여 스프루와 분리된다.
- 접촉 시간이 너무 길면 노즐부는 냉각되어 노즐 막힘이 발생한다.
2. 불량 현상 원인과 대책
미성형(충진부족, short shot)
- 성형품의 일부가 부족하게 되는 현상
- 사출압, 수지 온도가 낮아 유동성이 저하되므로 사출압과 수지 온도를 높이고 금형의 온도를 높인다.
- 사출량 부족의 경우 실린더 내의 사출 계량을 충분히 하여 공급량을 늘린다.
- 금형 구조성 스프루, 런너, 게이트가 너무 작을 때 압력 강하가 크게 되고 유동성이 나빠지므로 크게 한다.
바리(Burr, Flash)
- 성형품에 여분의 수지가 붙어있는 현상
- 금형의 파팅면이 좋지 않은 경우 금형의 코어면 등의 정밀도가 나쁘고 형합이 약하기 때문에 사출 압력으로 면이 내려앉아 틈이 생긴다.
- 금형의 강도가 부족하면 금형이 수지의 사출압에 의해 휘고, 제품이 두꺼워지거나 압력면을 따라 발생한다.
- 과다한 사출 압력과 유지시간이 긴 경우 가강 압력이 높아지는 게이트나 런너 부근에 flash가 발생한다.
- 형체압력 부족일 경우 성형품의 투영 면적에 비해서 형체력이 작으면 사출 압력에 의해 발생한다.
싱크 마크(Sink Mark)
- 성형품의 표면에 발생하는 오목 현상
- 제품의 두꺼운 부분이나 리브, 보스 등의 외측벽이 불충분한 냉각 때문에 충분히 안정되지 못하면 냉각 응력에 의해 바깥쪽 층이 안쪽으로 빨려 들어온다.
- 가장 기본적인 경우는 고화가 늦은 경우, 유효 보압 시간이 짧은 경우, 금형 내의 유동 저항이 너무 높기 때문에 충분한 보압이 전달되지 못한 경우이다.
- 스프루, 런너, 게이트가 작을 경우 크게 한다.
- 금형 온도의 조절이 부적합한 경우 높은 부분을 냉각한다.
- 사출압이 낮고 사출압 유지시간이 짧은 경우 발생할 수 있다.
성형 수축(Shrikage)
- 싱크 마크와는 다른 의미로 이는 제품 치수에 관계되는 현상이다.
- 제품 두께에 따라 성형 수축이 다르며 두꺼운 부분이 일반적으로 크다.
- 성형온도와 금형 온도가 높을수록 발생하기 쉽다.
- 보압과 사출 압력이 높을수록 수축이 작게 나타난다.
- 수지의 수분 흡수율 정도에 따라 치수가 달라질 수 있다.
웰드라인(Weld Line)
- 용융 수지가 금형 내를 분기해서 흐르다가 합류한 부분에 가는 선이 생기는 현상이다.
- 런너, 게이트가 너무 작을 경우 수지가 금형내 충전과정 중 유동 저항이 커서 유동성이 나빠지므로 런너, 게이트를 키워야 한다.
- 게이트가 웰드부까지의 거리가 긴 경우 수지의 온도 저하가 크므로 게이트를 추가 또는 위치를 바꾼다.
- 대책으로 수지 온도 및 금형 온도 상승과 사출 속도 및 사출 압력을 증가시킨다.
- 원재료의 충분한 건조가 필요하다. (Gas 발생 억제)
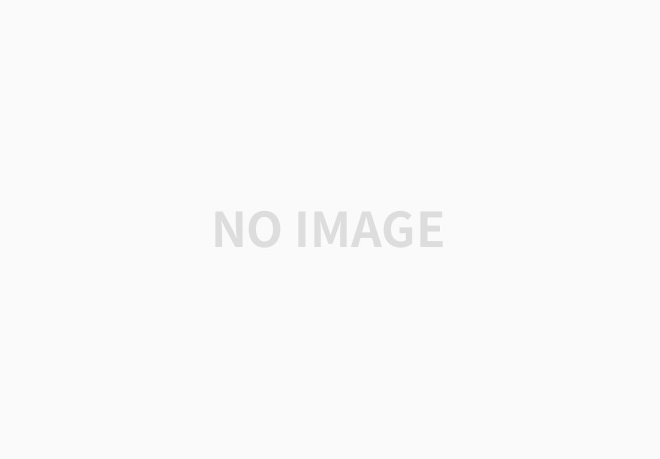
탄화(Burn)
- 수지나 가열성 휘발분 혹은 윤활제가 연소하여 제품에 검은 줄이 생기거나 수지가 탄화하여 검게 되는 현상이다.
- 게이트가 좁은 경우 압축에 의하여 큰 마찰열이 발생하고 수지가 과열 분해하므로 탄화가 발생한다. 게이트를 크게 하거나 수지 온도, 사출압, 사출 속도 등을 낮추면 좋다.
- 금형 표면에 묻어있는 기름 및 그리스가 나오는 경우 닦아주어야 한다.
- 실린더 온도가 높거나 사이클이 긴 경우에 성형을 할 때는 체류에 의한 열을 받기 때문에 수지 온도는 가능한 낮게 해야 한다.
- 호퍼 부근의 냉각이 불충분한 경우 수지의 공급이 나빠 공기를 빨아들여져 실린더에서 단열 압축으로 탄화가 일어나는 경우 실린더 온도를 낮춘다.
플로우 마크(Flow Mark)
- 성형 재료의 유동 궤적을 나타내는 줄무늬가 생기는 현상이다.
- 제품 형상이 전체적으로 고르게 냉각라인의 위치를 바꾼다.
- 수지 점도가 높은 경우 충분한 사출 압력을 전달할 수 없을 경우에 발생되므로 수지 및 금형 온도를 올리고 사출 속도를 빠르게 하여 점도 증가를 막는다.
- 기계적으로 플로우 컨트롤의 유량을 늘려 사출 속도를 빠르게 한다.
- 게이트 수를 늘려 흐름성을 쉽게 한다.
크랙(Crack)
- 성형품의 일부가 표면에 금이 가는 현상이다.
- 캐비티 과충전에 의한 경우 게이트 부근에 변형이 남아 크랙이 생기는 경우 수지의 유동성을 향상해 낮은 압력으로 충전할 수 있는 조건으로 한다.
- 주요 원인으로는 잔류 응력에 의한 경우, 외부 응력에 의한 경우, 환경 응력에 의한 경우가 있다.
- 금형 온도가 부적당한 경우 금형의 온도가 불균일할 경우 냉각 차에 의해 응력이 발생한다.
- 인서트 주위에는 인서트와 접하는 성형품의 두께 부족에 따른 응력 발생으로 크랙이 발생한다.
'사출성형' 카테고리의 다른 글
사출 금형 냉각 ① (0) | 2020.07.22 |
---|---|
사출성형 공정 관리 (0) | 2020.07.21 |
플라스틱의 이해 ① (0) | 2020.07.19 |
플라스틱 사출 성형해석의 이해 (0) | 2020.06.24 |
사출 성형 불량과 대책 (trouble shooting) ⑤ (0) | 2020.06.16 |
댓글