플라스틱의 정의
- 열이나 압력을 가했을 경우 용융되어 유동성을 가지는 물질로 좁은 의미에서 합성고분자 물질 또는 합성수지라고도 한다.
플라스틱의 장점
- 생산성이 높음
- 큰 부피의 제품 성형이 가능
- 자동화가 가능
- 제품의 별도 마무리 작업이 적음
- 자유로운 형상을 만들 수 있음
- 성형품에 다른 재료를 인서트 하여 가공 가능
- 수지에 보강제(유리섬유, 탄소섬유 등) 혼합 가능
플라스틱의 단점
- 금형 가격이 높음
- 성형 사출기 및 부대 장비의 가격이 높음
- 품질 확보 기간이 길어짐
- 사출성형 과정의 제어가 어려움
플라스틱의 특성
- 비중 : 0.8~2.0으로 유리나 금속에 비해 가볍다.(선박, 부표, 건축재료)
- 강도 : 금속에 비교할 만큼의 큰 강도를 가진 것도 있다.(볼트, 너트)
- 전기절연성 : 대부분 전기가 잘 통하지 않아서 절연성이 우수하다.(전기기구)
- 탄성 : 고무줄과 같이 잡아당기면 늘어나고 힘을 제거하면 원 상태로 돌아가는 성질의 탄성을 가지고 있다.(합성고무의 재료)
- 단열성 : 열을 차단하는 성질이 우수하다.(건축물의 단열재, 보온밥통)
- 광학적 성질 : 빚을 잘 통과시키는 투과성이 좋다.(전등케이스, 광학렌즈)
- 화학적 아정성 : 산이나 알카리 등의 화학약품에 부식이 되지 않는다.
- 내충격성 : 외부의 힘과 충격을 흡수하는 성질이 있다.(헬멧)
열가소성 수지
- 열을 가해 완성된 제품을 만든 뒤에 다시 열이나 압력을 가하여 다른 모양의 제품 성형 가능
- 종류 : 폴리에틸렌(PE), 폴리프로필렌(PP), 폴리아미드(PA)
- 재생 가능한 수지
열경화성 수지
- 열에 의해 한번 굳어진 다음에 다시 가열해도 성형 불가함
- 종류 : 페놀, 에폭시, 우레탄
- 재생 불가능한 수지
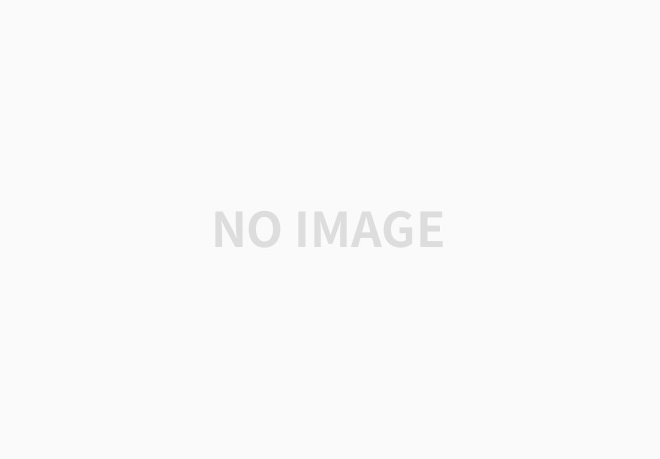
PP (Poly Propylene)
- 비중이 낮고 가격이 싸며 반복 휨이 강함
- 결정성 수지로서 유연한 재질
- 치수 안정성, 도장성, 접착 성능 불량
PE (Poly Ethylene)
- 유연성, 내수성, 전지 절연성 우수
- 충격성 우수하고 화학적으로 매우 안정적
ABS (Acrylonitrile Butadiene Styrene)
- 인장강도, 충격 강도 우수
- 기계적 특성이 우수 (고경도, 고강도)
- 도장 및 도금 성능이 우수
PVC (Poly Vinyl Chloride)
- 플라스틱 중 가장 점도가 높고 열 안전성이 나쁨
- 내 노화성 및 자소성이 우수
- 내열 및 내한성이 약함
PC (Poly Carbonate)
- 강도, 내충격성, 투명성, 내스크래치성이 우수
- 내열성, 전기적 성질 우수, 내약품성 불량
- 성형 시 수분에 의한 물성 저하
PU (Poly Urethane)
- 발포 고분자
- 내마모성이 우수
- 인조가죽 소재
PBT (Poly Butylene Terephthalate)
- 기계적 강도, 내열성, 치수안전성 우수
- 내약품성, 전기적 특성, 자기 소화성 우수
- Notch에 민감, 성형 시 물성 저하
TPO (Thermo Plastic Elastomer Olefine)
- 비중이 작고, 내열 노화성, 내한성 우수
- 내후성, 전기적 특성 양호
- 내유성, 난연성, 접착성 등이 불량
POM (Poly Oxymethylene, Acetal)
- 기계적 특성, 내마모성, 내마찰성 우수
- 내약품성, 내알칼리성 우수
- 플라스틱 중 최고의 내피로성, 자기 윤활성
PA (Poly Amide, Nylon)
- 내마모성, 내마찰성, 내후성, 내유성 우수
- 후변형, 흡수성이 강함
- 내열성, 내약품성, 절연 특성이 양호
PMMA (Poly Methyl Methacrylate, Acrylic)
- 플라스틱 중에서 투명성이 가장 뛰어남
- 최고의 경도 (알루미늄과 유사한 경도)
- 유동성이 좋지 않아 사출압은 고압이 필요
복합 재료 (Composite)
- 플라스틱 원소재에 보장재를 넣어 기능(물성, 강도)을 증가시킨 재료
- 주로 유리섬유, 탈크가 가장 많이 사용됨
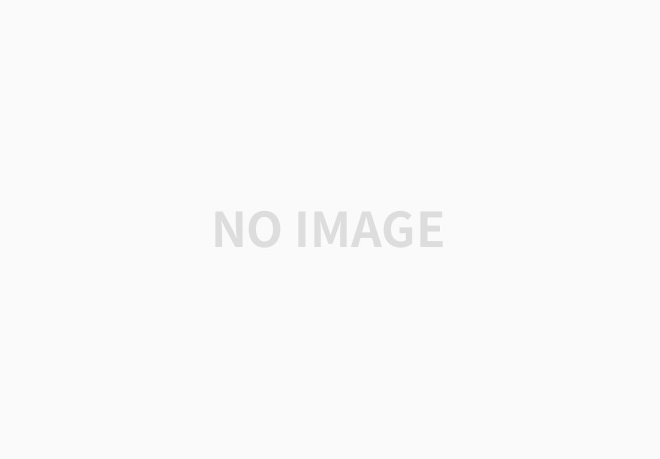
금형 구조 및 용어
- 스프루 부시 : 사출기의 노즐로부터 용융 플라스틱을 공급받아 금형의 캐비티 내에 충전시키는 입구
- 로케이트 링 : 사출기의 노줄과 금형의 스프루 부시의 Hole을 일치시키기 위해 상측 고정판에 고정된 링(Ring)
- 상고정판 : 금형을 구성하는 맨 위에 있는 판으로 사출성형 장비의 고정측 부착판에 금형을 설치하여 고정하는 판
- 상원판 : 제품의 외관(Skin)을 결정하는 형판
- 하원판 : 제품의 배면을 결정하는 형판
- 받침판 : 하원판 밑면을 받쳐주는 보강판으로 사출성형 시 고압으로 가동측 형판에 휨이 일어나지 않게 받쳐주는 판
- 스페이스 블록 : 받침판과 하고정판 사이에 설치하여 이젝트 플레이트가 작동할 수 있는 공간을 만들어 주는 장치
- 밀판 : 제품을 취출 하기 위하여 밀핀 등을 고정하는 판 (상밀판, 하밀판으로 구성)
- 하고정판 : 금형을 구성하는 맨 아래에 있는 판으로 사출성형 장비의 가동측 부착판에 금형을 설치하여 고정하는 판
플라스틱 성형공법
- 사출성형 : 금형 안에 용융 플라스틱을 고압으로 주입하여 정밀한 성형품을 가공하는 방법
- 중공성형 : 가소화된 파이프 모양의 Parison을 외형만으로 이루어진 금형 안에 삽입하고 압축공기를 불어넣어 팽창시켜 성형하는 공법
- 압출성형 : 용융 플라스틱에 압력을 가하여 Die를 통과시켜 연속적으로 성형하는 방법
- 압축성형 : Sheet재 또는 경단재의 재료를 형내에 넣어 성형하는 방법으로 형을 고온(120~160도)으로 하여 그 열에 의해 성형하는 공법
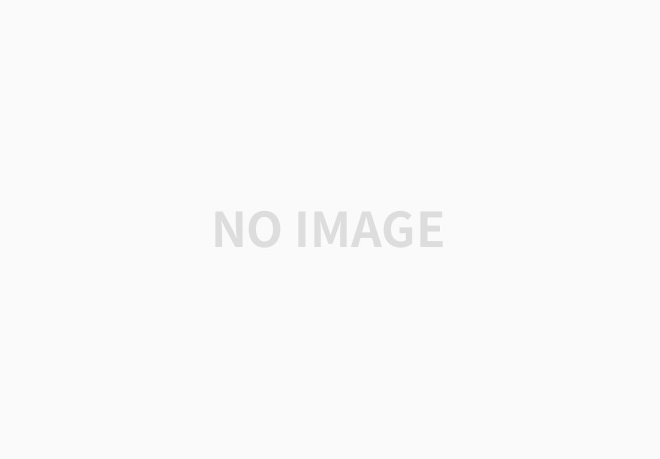
사출기의 기본 구조
- 형체 장치 : 금형을 장착하여 금형을 여닫을 수 있게 하고, 성형품을 빼낼 수 있는 장치 (금형 설치판, 타이바, 형체 실린더, 이젝터)
- 사출 장치 : 1회 사출에 필요한 재료를 계량하고 용융시켜 금형 안으로 유입시키는 장치 (스크루, 노즐, 호퍼, 히터 등)
- 유압 장치 : 각종 실린더 작동이나 스크루의 회전등의 구동에 필요한 압력을 만들고 전달하는 장치 (유압펌프, 배관, 유압모터)
- 전기 장치 : 사출장치나 형체 장치의 동작과 가열 실린더 및 노즐의 온도를 제어 (제어반)
유압식 사출기
- 작동 파워로 유압을 사용
- 장점 : 장비 소요 면적이 적음, 다른 타입 대비 가격이 상대적으로 낮음
- 단점 : 유압 모터 지속 가동으로 소비전력량 높음, 유압 사용으로 작동유 및 냉감수 사용 필요함(추가 유지 비용 발생), 작동유 누유 등에 의한 청결관리 어려움, 작동유 상태(온도, 점도 등) 문제시 솔레노이드 밸브 트러블 발생
전동식 사출기
- 전 구동부에 전동 모터 사용, 전동모터로 유압식 사출기의 형체력 구현 불가로 토글식 형체 구조 사용
- 장점 : 전체 전동 제어로 정밀 제어 가능, 외부 영향 적으며 제품 재현성 우수함, 전동 모터 고속 제어로 사이클 타임 단축됨, 작동유 및 냉각수 미사용으로 유지비 절감, 서보 모터 적용으로 전력비 절감, 기존 유압 대비 기구부 전기장치 사용으로 문제점 확인 및 보수 용이함
- 단점 : 토글식으로 장비 소요 면적이 넓음, 금형 코어 작동용 별도 유압펌프 필요함
Hybrid 사출기
- 형체 측만 유압을 사용, 기타 부위 전동모터 사용
- 장점 : 형체 발생부 외 서보 모터 제어로 정밀 제어 가능함, 직압식으로 전동사출기 대비 소요 면적 적음
- 단점 : 형체를 위한 유압 모터 지속 가동으로 소요 전력량이 전동식 대비 높음, 작동유 및 냉각수 사용으로 추가 유지비 발생, 형체부 작동유 사용으로 정밀 형체 제어 어려우며 청결관리 어려움
'사출성형' 카테고리의 다른 글
사출성형 공정 관리 (0) | 2020.07.21 |
---|---|
플라스틱의 이해 ② (0) | 2020.07.20 |
플라스틱 사출 성형해석의 이해 (0) | 2020.06.24 |
사출 성형 불량과 대책 (trouble shooting) ⑤ (0) | 2020.06.16 |
사출 성형 불량과 대책 (trouble shooting) ④ (0) | 2020.06.11 |
댓글